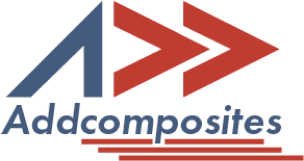
In the realm of advanced manufacturing, the quest for materials that are both lightweight and incredibly strong has led to groundbreaking innovations. Among these, Variable Stiffness Composites (VSC) stand out as a beacon of technological advancement. But how do we tackle the complex manufacturing challenges that come with such sophisticated materials? This is where the pioneering research of L.T. Tunc and M. Sheikhi from Sabanci University comes into play, reshaping the future of composite manufacturing.
In this comprehensive exploration, we delve into their revolutionary approach to Automated Fiber Placement (AFP) tool path planning for VSC. Their novel methodology not only addresses key manufacturing challenges, like wrinkles, gaps, and overlaps, but also significantly enhances the performance and quality of composite products. From the intricate details of their path planning algorithm to the practical applications demonstrated through case studies, this blog is a deep dive into the future of advanced composite manufacturing.
Variable Stiffness Composites (VSC) represent a significant evolution in composite materials, building upon the foundation set by Carbon Fiber Reinforced Plastics (CFRP). Since the 1960s, CFRP has been a cornerstone in high-strength, lightweight applications, particularly in aerospace, automotive, and marine industries. Its high strength-to-weight ratio has been indispensable for sustainable, high-value manufacturing. However, the conventional manufacturing of CFRP, often involving manual layup for large parts such as aircraft wings, has limitations in terms of time, cost, and the level of skill required.
VSC steps in to address these challenges and push the boundaries further. Unlike CFRP, which traditionally employs constant direction lay-up, VSC allows for the alignment of fibers in varying, optimized directions. This capability stems from advancements in automated fiber placement (AFP) technology and the integration of sophisticated finite element analysis (FEA). By aligning fibers with the load direction, VSC leverages the anisotropic mechanical properties of the composites to a greater extent than is possible with CFRP.
Conventional vs proposed approach, (a) constant angle path planning, (b) streamline path planning, (c) cluster-based path planning. *M: Manufacturability, D: Design.
The anisotropic nature of VSC enables them to exhibit enhanced mechanical properties. The key lies in their ability to align fibers in accordance with the load directions—a feature not fully exploited in CFRP due to its constant direction lay-up approach. This alignment is critical in maximizing performance, particularly in applications where directional stresses are predominant. FEA plays a crucial role in optimizing these fiber directions, ensuring that the VSC components are not only stronger but also more efficient in handling applied loads.
The manufacturing of Variable Stiffness Composites (VSC) introduces unique challenges, particularly in the context of Automated Fiber Placement (AFP) tool path generation. AFP, a key technological advancement in composite manufacturing, involves laying down composite tows (bundles of fibers) onto a mold or a form using a robotic system. This process, while automated, demands precise control and optimization to ensure quality and integrity of the final product.
Defects in AFP, (a) parallel offset, (b) shift offset, (c) wrinkles and gaps, (d) wandering tow, (e) overlaps, (f) waviness
One of the critical challenges in AFP is managing potential manufacturing defects. As the fibers are laid down, issues such as wrinkles, gaps, and overlaps can occur, significantly impacting the mechanical performance and structural integrity of the composite. These defects are not just superficial; they can lead to weak points in the material, which might compromise its ability to withstand loads and stresses.
Precise tool path planning is essential to mitigate these defects. In the manufacture of VSC, the complexity is heightened due to the variable steering of fiber directions. This variable steering, while beneficial for aligning fibers with load directions, introduces additional challenges in maintaining the continuity and consistency of fiber layup. The research highlights the importance of conforming the tool path to optimized layup directions to achieve the desired mechanical performance.
To address these challenges, the paper discusses innovative path planning algorithms that integrate finite element analysis (FEA) to optimize fiber directions. This approach ensures that manufacturing constraints are enforced, controlling layup defects and maintaining the integrity of the VSC. The research underscores the need for continuous innovation in AFP technology to keep pace with the evolving demands of composite manufacturing.
The manufacturing of Variable Stiffness Composites (VSC) requires innovative approaches in tool path planning, especially in the context of Automated Fiber Placement (AFP). In the research by L.T. Tunc and M. Sheikhi, a groundbreaking path planning algorithm is introduced, aimed at revolutionizing the AFP process. This novel algorithm is specifically designed for variable steering in AFP, a crucial aspect in the fabrication of VSC.
A key component of this innovative approach is the optimization of fiber directions using Finite Element Analysis (FEA). FEA enables the precise calculation of optimal fiber orientations based on various mechanical properties, such as strain energy, buckling, or natural frequency. This optimization is critical in ensuring that the VSC components can achieve the highest levels of performance and strength, tailored to specific application needs.
Another significant advancement presented in the paper is the use of B-Spline for fitting reference curves. Once the fiber directions are determined through FEA, each cluster of fibers is assigned a reference curve fitted as a B-Spline. This technique allows for a more controlled and accurate placement of fibers, addressing one of the primary challenges in AFP – maintaining precision in variable steering paths. The B-Spline fitting ensures that the tool path adheres closely to the optimized fiber directions, thus minimizing potential defects and maximizing the mechanical properties of the composite.
The integration of this novel path planning algorithm, combined with FEA optimization and B-Spline curve fitting, marks a significant leap forward in the manufacturing of VSC. It addresses key challenges such as maintaining fiber orientation, controlling manufacturing defects, and ensuring the structural integrity of the composites. This approach not only enhances the quality of the final product but also broadens the potential applications of VSC in various industries, including aerospace, automotive, and marine.
The research by L.T. Tunc and M. Sheikhi includes case studies that are instrumental in demonstrating the practical application and effectiveness of their novel AFP tool path planning algorithm for Variable Stiffness Composites (VSC). These case studies provide real-world scenarios where the proposed method can be applied, showcasing its versatility and impact on composite manufacturing.
One notable case study mentioned in the paper involves the application of the novel path planning approach to a multi-layered, simply supported plate. This case study is crucial in demonstrating how the algorithm can be implemented in a real AFP system. The researchers used thermoset CFRP slit tapes with specific fiber bundles and weight parameters, ensuring the study's relevance to actual manufacturing conditions.
The results from these case studies validate the effectiveness of the proposed tool path planning approach. Key findings include the successful implementation of the novel algorithm in an AFP system, demonstrating its practicality and scalability. The case studies also highlight the algorithm's ability to optimize fiber directions effectively, as evidenced by the enhanced mechanical properties of the produced VSC.
The research presented by L.T. Tunc and M. Sheikhi marks a significant advancement in the manufacturing of Variable Stiffness Composites (VSC). The development of a novel tool path planning algorithm for Automated Fiber Placement (AFP) addresses some of the most pressing challenges in composite manufacturing. This research not only demonstrates the feasibility of producing higher quality VSC products but also shows a clear path to enhancing their performance. The innovative approach to fiber placement and optimization, leveraging Finite Element Analysis (FEA) and B-Spline curve fitting, ensures that the VSC products are not only stronger but also more consistent and reliable.
Looking forward, this research opens up several avenues for further exploration and innovation in the field of composite manufacturing. One potential direction is the refinement of the tool path planning algorithm to further minimize manufacturing defects such as gaps, overlaps, and wrinkles. Additionally, exploring the integration of more advanced computational methods and machine learning techniques could offer even more precise control and optimization of fiber placement.
Another promising area is the application of this technology to a wider range of composite materials and structures. As the demand for lightweight yet strong materials continues to grow in industries such as aerospace, automotive, and marine, the importance of advanced manufacturing techniques like those developed in this research will only increase.
For those interested in exploring more about AFP, VSC, and advanced manufacturing technologies, the following resources provide in-depth information and insights:
Discover the future of composite manufacturing with Addcomposites! Here's how you can get involved:
At Addcomposites, we are dedicated to revolutionizing composite manufacturing. Our AFP systems and comprehensive support services are waiting for you to harness. So, don't wait – get started on your journey to the future of manufacturing today!
In the realm of advanced manufacturing, the quest for materials that are both lightweight and incredibly strong has led to groundbreaking innovations. Among these, Variable Stiffness Composites (VSC) stand out as a beacon of technological advancement. But how do we tackle the complex manufacturing challenges that come with such sophisticated materials? This is where the pioneering research of L.T. Tunc and M. Sheikhi from Sabanci University comes into play, reshaping the future of composite manufacturing.
In this comprehensive exploration, we delve into their revolutionary approach to Automated Fiber Placement (AFP) tool path planning for VSC. Their novel methodology not only addresses key manufacturing challenges, like wrinkles, gaps, and overlaps, but also significantly enhances the performance and quality of composite products. From the intricate details of their path planning algorithm to the practical applications demonstrated through case studies, this blog is a deep dive into the future of advanced composite manufacturing.
Variable Stiffness Composites (VSC) represent a significant evolution in composite materials, building upon the foundation set by Carbon Fiber Reinforced Plastics (CFRP). Since the 1960s, CFRP has been a cornerstone in high-strength, lightweight applications, particularly in aerospace, automotive, and marine industries. Its high strength-to-weight ratio has been indispensable for sustainable, high-value manufacturing. However, the conventional manufacturing of CFRP, often involving manual layup for large parts such as aircraft wings, has limitations in terms of time, cost, and the level of skill required.
VSC steps in to address these challenges and push the boundaries further. Unlike CFRP, which traditionally employs constant direction lay-up, VSC allows for the alignment of fibers in varying, optimized directions. This capability stems from advancements in automated fiber placement (AFP) technology and the integration of sophisticated finite element analysis (FEA). By aligning fibers with the load direction, VSC leverages the anisotropic mechanical properties of the composites to a greater extent than is possible with CFRP.
Conventional vs proposed approach, (a) constant angle path planning, (b) streamline path planning, (c) cluster-based path planning. *M: Manufacturability, D: Design.
The anisotropic nature of VSC enables them to exhibit enhanced mechanical properties. The key lies in their ability to align fibers in accordance with the load directions—a feature not fully exploited in CFRP due to its constant direction lay-up approach. This alignment is critical in maximizing performance, particularly in applications where directional stresses are predominant. FEA plays a crucial role in optimizing these fiber directions, ensuring that the VSC components are not only stronger but also more efficient in handling applied loads.
The manufacturing of Variable Stiffness Composites (VSC) introduces unique challenges, particularly in the context of Automated Fiber Placement (AFP) tool path generation. AFP, a key technological advancement in composite manufacturing, involves laying down composite tows (bundles of fibers) onto a mold or a form using a robotic system. This process, while automated, demands precise control and optimization to ensure quality and integrity of the final product.
Defects in AFP, (a) parallel offset, (b) shift offset, (c) wrinkles and gaps, (d) wandering tow, (e) overlaps, (f) waviness
One of the critical challenges in AFP is managing potential manufacturing defects. As the fibers are laid down, issues such as wrinkles, gaps, and overlaps can occur, significantly impacting the mechanical performance and structural integrity of the composite. These defects are not just superficial; they can lead to weak points in the material, which might compromise its ability to withstand loads and stresses.
Precise tool path planning is essential to mitigate these defects. In the manufacture of VSC, the complexity is heightened due to the variable steering of fiber directions. This variable steering, while beneficial for aligning fibers with load directions, introduces additional challenges in maintaining the continuity and consistency of fiber layup. The research highlights the importance of conforming the tool path to optimized layup directions to achieve the desired mechanical performance.
To address these challenges, the paper discusses innovative path planning algorithms that integrate finite element analysis (FEA) to optimize fiber directions. This approach ensures that manufacturing constraints are enforced, controlling layup defects and maintaining the integrity of the VSC. The research underscores the need for continuous innovation in AFP technology to keep pace with the evolving demands of composite manufacturing.
The manufacturing of Variable Stiffness Composites (VSC) requires innovative approaches in tool path planning, especially in the context of Automated Fiber Placement (AFP). In the research by L.T. Tunc and M. Sheikhi, a groundbreaking path planning algorithm is introduced, aimed at revolutionizing the AFP process. This novel algorithm is specifically designed for variable steering in AFP, a crucial aspect in the fabrication of VSC.
A key component of this innovative approach is the optimization of fiber directions using Finite Element Analysis (FEA). FEA enables the precise calculation of optimal fiber orientations based on various mechanical properties, such as strain energy, buckling, or natural frequency. This optimization is critical in ensuring that the VSC components can achieve the highest levels of performance and strength, tailored to specific application needs.
Another significant advancement presented in the paper is the use of B-Spline for fitting reference curves. Once the fiber directions are determined through FEA, each cluster of fibers is assigned a reference curve fitted as a B-Spline. This technique allows for a more controlled and accurate placement of fibers, addressing one of the primary challenges in AFP – maintaining precision in variable steering paths. The B-Spline fitting ensures that the tool path adheres closely to the optimized fiber directions, thus minimizing potential defects and maximizing the mechanical properties of the composite.
The integration of this novel path planning algorithm, combined with FEA optimization and B-Spline curve fitting, marks a significant leap forward in the manufacturing of VSC. It addresses key challenges such as maintaining fiber orientation, controlling manufacturing defects, and ensuring the structural integrity of the composites. This approach not only enhances the quality of the final product but also broadens the potential applications of VSC in various industries, including aerospace, automotive, and marine.
The research by L.T. Tunc and M. Sheikhi includes case studies that are instrumental in demonstrating the practical application and effectiveness of their novel AFP tool path planning algorithm for Variable Stiffness Composites (VSC). These case studies provide real-world scenarios where the proposed method can be applied, showcasing its versatility and impact on composite manufacturing.
One notable case study mentioned in the paper involves the application of the novel path planning approach to a multi-layered, simply supported plate. This case study is crucial in demonstrating how the algorithm can be implemented in a real AFP system. The researchers used thermoset CFRP slit tapes with specific fiber bundles and weight parameters, ensuring the study's relevance to actual manufacturing conditions.
The results from these case studies validate the effectiveness of the proposed tool path planning approach. Key findings include the successful implementation of the novel algorithm in an AFP system, demonstrating its practicality and scalability. The case studies also highlight the algorithm's ability to optimize fiber directions effectively, as evidenced by the enhanced mechanical properties of the produced VSC.
The research presented by L.T. Tunc and M. Sheikhi marks a significant advancement in the manufacturing of Variable Stiffness Composites (VSC). The development of a novel tool path planning algorithm for Automated Fiber Placement (AFP) addresses some of the most pressing challenges in composite manufacturing. This research not only demonstrates the feasibility of producing higher quality VSC products but also shows a clear path to enhancing their performance. The innovative approach to fiber placement and optimization, leveraging Finite Element Analysis (FEA) and B-Spline curve fitting, ensures that the VSC products are not only stronger but also more consistent and reliable.
Looking forward, this research opens up several avenues for further exploration and innovation in the field of composite manufacturing. One potential direction is the refinement of the tool path planning algorithm to further minimize manufacturing defects such as gaps, overlaps, and wrinkles. Additionally, exploring the integration of more advanced computational methods and machine learning techniques could offer even more precise control and optimization of fiber placement.
Another promising area is the application of this technology to a wider range of composite materials and structures. As the demand for lightweight yet strong materials continues to grow in industries such as aerospace, automotive, and marine, the importance of advanced manufacturing techniques like those developed in this research will only increase.
For those interested in exploring more about AFP, VSC, and advanced manufacturing technologies, the following resources provide in-depth information and insights:
Discover the future of composite manufacturing with Addcomposites! Here's how you can get involved:
At Addcomposites, we are dedicated to revolutionizing composite manufacturing. Our AFP systems and comprehensive support services are waiting for you to harness. So, don't wait – get started on your journey to the future of manufacturing today!