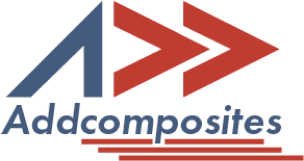
Welcome to our deep dive into the world of Automated Fiber Deposition (AFD) and its transformative impact on aerospace manufacturing. Before we delve into the details, let's give you a quick teaser of what you're about to explore in this blog:
This blog aims to provide a comprehensive understanding of AFD’s role in the aerospace industry, highlighting its current state, challenges, and the exciting possibilities it holds for the future. Whether you’re a professional in the field, a student of aerospace engineering, or simply an enthusiast for cutting-edge manufacturing technologies, this exploration will offer valuable insights into how AFD is shaping the future of aerospace manufacturing. Let’s embark on this journey to uncover the intricate and fascinating world of Automated Fiber Deposition.
In the high-stakes realm of aerospace engineering, the demand for manufacturing processes that are both highly efficient and precise is paramount. AFD emerges as a critical technology in meeting these demands. AFD allows for the precise placement of fibers in composite materials, an essential factor in aerospace applications where every millimeter counts. This technology enables manufacturers to design and produce components with complex shapes and intricate details, which were previously challenging or impossible with traditional methods.
The precision of AFD is not just about accuracy in shaping; it's also about material efficiency. By placing fibers exactly where they are needed, AFD minimizes material wastage. In an industry where reducing the weight of components can lead to significant fuel savings, the ability to use materials judiciously is a game-changer.
The aerospace industry constantly seeks ways to improve the performance of its components, and AFD plays a crucial role in this pursuit. By controlling fiber orientation and placement, AFD allows for the creation of parts that are not only lighter but also stronger and more durable. This is particularly important in aerospace, where the strength-to-weight ratio of materials can significantly impact the performance and efficiency of aircraft.
AFD technology enables the fabrication of composite materials that can withstand extreme stresses and temperatures, common in aerospace environments. This results in components that offer enhanced performance, contributing to safer, more reliable, and more efficient aircraft.
Sustainability is an ever-growing concern in the aerospace industry, and AFD technology contributes positively in this area. By reducing material waste and enabling the use of recycled materials, AFD promotes a greener manufacturing process. The precision of fiber placement means that less raw material is required, leading to a reduction in the overall environmental footprint of manufacturing.
Moreover, the lightweight components produced through AFD contribute to more fuel-efficient aircraft, which in turn leads to lower emissions. This aspect is crucial as the aerospace industry moves towards more sustainable practices and aims to meet global environmental targets.
AFD is a sophisticated manufacturing process that has revolutionized the way aerospace components are made. Here's a closer look at how it works:
AFD technology involves the automated placement of fiber-reinforced materials onto a mold or form to create complex structures. This process is often computer-controlled, allowing for precise manipulation of fiber angles and positions. It's particularly useful for creating composite materials, which are central to modern aerospace design due to their high strength-to-weight ratio.
The basic principle of AFD involves feeding fiber tapes or tows through a deposition head. This head is mounted on a robotic arm or gantry system that can move in multiple directions. As the fibers are laid down, they are often simultaneously heated to bond with the underlying layer or matrix material, ensuring a strong and cohesive build.
The 2023 highlights key advancements in AFD technology, particularly in the realm of aerospace applications. A significant innovation is the development of a novel programming and data storage paradigm. This advancement allows for the creation of a 'digital twin' of the manufacturing process. With a digital twin, there’s bi-directional communication between the designed part and the manufactured part, facilitating real-time process control, online in-process quality control, and seamless integration with resin flow and structural simulations.
Another critical development is the 'Fibre-steered forming technology (FSF)', designed for high-volume production of small and complex composite parts. This technology, which combines virtual unforming simulation, HiPerDiF process, and Continuous Tow Shearing (CTS), allows for the designing of 2D fiber-steered preforms that can be transformed into complex 3D shapes. This innovation addresses the limitations of current Automated Fiber Placement (AFP) processes in manufacturing small and intricate parts.
In aerospace, AFD technology has been employed in manufacturing various components such as wing spars, fuselage sections, and other critical structural parts. The precise control over fiber orientation that AFD offers translates into parts that can withstand the unique stresses and demands of aerospace applications. These components are not only lighter and stronger but also more uniform in quality compared to those produced by traditional methods.
AFD technology has significantly impacted the aerospace industry. However, like any advanced technology, it comes with its own set of advantages and challenges. Understanding these can provide insights into its applicability and future development.
The future of AFD in aerospace looks promising, with ongoing advancements and potential applications poised to further revolutionize this sector. Here's an exploration of what the future holds for AFD technology in aerospace:
The advancements in AFD technology have the potential to transform aerospace manufacturing significantly. By enabling the production of lighter, stronger, and more complex components, AFD can contribute to the development of next-generation aircraft that are more efficient and environmentally friendly. This technology's evolution will likely lead to new design paradigms in aerospace engineering, where limitations of traditional manufacturing methods no longer constrain innovation.
AFD technology is at the forefront of a manufacturing revolution in the aerospace industry. Its ability to create high-quality, complex components efficiently and sustainably aligns well with the industry's future direction. As this technology continues to evolve, its impact on aerospace design, manufacturing, and performance is expected to be substantial, paving the way for more innovative, efficient, and sustainable air travel.
As we conclude this insightful journey through the world of Automated Fiber Deposition in aerospace, we extend our heartfelt thanks to the authors and contributors of the CIMComp Annual Report 2023. Their diligent research and comprehensive analysis have been instrumental in providing the foundational material for this blog.
Their work not only sheds light on the current advancements in AFD technology but also sparks imagination and curiosity about the future possibilities in aerospace manufacturing. We are deeply grateful for their contributions to the field and for making such valuable information accessible, which has greatly enriched the content and depth of our discussion in this blog.
To the authors and everyone involved in the creation of the CIMComp Annual Report 2023, thank you for your invaluable contributions to the aerospace industry and for inspiring discussions like these. Your work continues to drive innovation and progress in aerospace technologies, shaping the future of this exciting and ever-evolving field.
Discover the future of composite manufacturing with Addcomposites! Here's how you can get involved:
At Addcomposites, we are dedicated to revolutionizing composite manufacturing. Our AFP systems and comprehensive support services are waiting for you to harness. So, don't wait – get started on your journey to the future of manufacturing today!
Welcome to our deep dive into the world of Automated Fiber Deposition (AFD) and its transformative impact on aerospace manufacturing. Before we delve into the details, let's give you a quick teaser of what you're about to explore in this blog:
This blog aims to provide a comprehensive understanding of AFD’s role in the aerospace industry, highlighting its current state, challenges, and the exciting possibilities it holds for the future. Whether you’re a professional in the field, a student of aerospace engineering, or simply an enthusiast for cutting-edge manufacturing technologies, this exploration will offer valuable insights into how AFD is shaping the future of aerospace manufacturing. Let’s embark on this journey to uncover the intricate and fascinating world of Automated Fiber Deposition.
In the high-stakes realm of aerospace engineering, the demand for manufacturing processes that are both highly efficient and precise is paramount. AFD emerges as a critical technology in meeting these demands. AFD allows for the precise placement of fibers in composite materials, an essential factor in aerospace applications where every millimeter counts. This technology enables manufacturers to design and produce components with complex shapes and intricate details, which were previously challenging or impossible with traditional methods.
The precision of AFD is not just about accuracy in shaping; it's also about material efficiency. By placing fibers exactly where they are needed, AFD minimizes material wastage. In an industry where reducing the weight of components can lead to significant fuel savings, the ability to use materials judiciously is a game-changer.
The aerospace industry constantly seeks ways to improve the performance of its components, and AFD plays a crucial role in this pursuit. By controlling fiber orientation and placement, AFD allows for the creation of parts that are not only lighter but also stronger and more durable. This is particularly important in aerospace, where the strength-to-weight ratio of materials can significantly impact the performance and efficiency of aircraft.
AFD technology enables the fabrication of composite materials that can withstand extreme stresses and temperatures, common in aerospace environments. This results in components that offer enhanced performance, contributing to safer, more reliable, and more efficient aircraft.
Sustainability is an ever-growing concern in the aerospace industry, and AFD technology contributes positively in this area. By reducing material waste and enabling the use of recycled materials, AFD promotes a greener manufacturing process. The precision of fiber placement means that less raw material is required, leading to a reduction in the overall environmental footprint of manufacturing.
Moreover, the lightweight components produced through AFD contribute to more fuel-efficient aircraft, which in turn leads to lower emissions. This aspect is crucial as the aerospace industry moves towards more sustainable practices and aims to meet global environmental targets.
AFD is a sophisticated manufacturing process that has revolutionized the way aerospace components are made. Here's a closer look at how it works:
AFD technology involves the automated placement of fiber-reinforced materials onto a mold or form to create complex structures. This process is often computer-controlled, allowing for precise manipulation of fiber angles and positions. It's particularly useful for creating composite materials, which are central to modern aerospace design due to their high strength-to-weight ratio.
The basic principle of AFD involves feeding fiber tapes or tows through a deposition head. This head is mounted on a robotic arm or gantry system that can move in multiple directions. As the fibers are laid down, they are often simultaneously heated to bond with the underlying layer or matrix material, ensuring a strong and cohesive build.
The 2023 highlights key advancements in AFD technology, particularly in the realm of aerospace applications. A significant innovation is the development of a novel programming and data storage paradigm. This advancement allows for the creation of a 'digital twin' of the manufacturing process. With a digital twin, there’s bi-directional communication between the designed part and the manufactured part, facilitating real-time process control, online in-process quality control, and seamless integration with resin flow and structural simulations.
Another critical development is the 'Fibre-steered forming technology (FSF)', designed for high-volume production of small and complex composite parts. This technology, which combines virtual unforming simulation, HiPerDiF process, and Continuous Tow Shearing (CTS), allows for the designing of 2D fiber-steered preforms that can be transformed into complex 3D shapes. This innovation addresses the limitations of current Automated Fiber Placement (AFP) processes in manufacturing small and intricate parts.
In aerospace, AFD technology has been employed in manufacturing various components such as wing spars, fuselage sections, and other critical structural parts. The precise control over fiber orientation that AFD offers translates into parts that can withstand the unique stresses and demands of aerospace applications. These components are not only lighter and stronger but also more uniform in quality compared to those produced by traditional methods.
AFD technology has significantly impacted the aerospace industry. However, like any advanced technology, it comes with its own set of advantages and challenges. Understanding these can provide insights into its applicability and future development.
The future of AFD in aerospace looks promising, with ongoing advancements and potential applications poised to further revolutionize this sector. Here's an exploration of what the future holds for AFD technology in aerospace:
The advancements in AFD technology have the potential to transform aerospace manufacturing significantly. By enabling the production of lighter, stronger, and more complex components, AFD can contribute to the development of next-generation aircraft that are more efficient and environmentally friendly. This technology's evolution will likely lead to new design paradigms in aerospace engineering, where limitations of traditional manufacturing methods no longer constrain innovation.
AFD technology is at the forefront of a manufacturing revolution in the aerospace industry. Its ability to create high-quality, complex components efficiently and sustainably aligns well with the industry's future direction. As this technology continues to evolve, its impact on aerospace design, manufacturing, and performance is expected to be substantial, paving the way for more innovative, efficient, and sustainable air travel.
As we conclude this insightful journey through the world of Automated Fiber Deposition in aerospace, we extend our heartfelt thanks to the authors and contributors of the CIMComp Annual Report 2023. Their diligent research and comprehensive analysis have been instrumental in providing the foundational material for this blog.
Their work not only sheds light on the current advancements in AFD technology but also sparks imagination and curiosity about the future possibilities in aerospace manufacturing. We are deeply grateful for their contributions to the field and for making such valuable information accessible, which has greatly enriched the content and depth of our discussion in this blog.
To the authors and everyone involved in the creation of the CIMComp Annual Report 2023, thank you for your invaluable contributions to the aerospace industry and for inspiring discussions like these. Your work continues to drive innovation and progress in aerospace technologies, shaping the future of this exciting and ever-evolving field.
Discover the future of composite manufacturing with Addcomposites! Here's how you can get involved:
At Addcomposites, we are dedicated to revolutionizing composite manufacturing. Our AFP systems and comprehensive support services are waiting for you to harness. So, don't wait – get started on your journey to the future of manufacturing today!