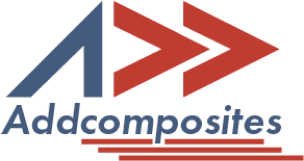
Thermoplastic composites are increasingly being used in a wide range of applications, from aerospace to automotive and beyond, due to their superior strength, durability, and weight-saving properties. However, producing high-quality thermoplastic composite parts requires precision and control at every step of the manufacturing process. The Automated Fiber Placement (AFP) process by Addcomposites has been instrumental in achieving this precision and control, and the latest version, the AFP-XS, has brought even more advancements in the field. In this blog post, we will explore three key features of the AFP-XS that have improved the controls and quality of thermoplastic composite parts: improved turning and on/off control for a tab-free layup, built-in tilt control for higher exposure and high-temperature thermoplastic layup, and a cooled compaction roller for longevity. Let's dive in!
The AFP-XS by Addcomposites is designed to provide improved turning and on/off control for a tab-free layup. Usually, in order to avoid the burning of the compaction roller or sudden heating of the initial portion of the tab, tapes are fed without any heat. However, with the heating control setup provided by AddPath, the AFP-XS enables millisecond level control of delay to heat the initial tapes exactly at the point that allows for the right amount of heating of the tabs and not burn the roller, eliminating the need for tabs.
The heating control allows for triggering heating on and off at each step of the program, with built-in delays to ensure precise control. These steps include before the approach path, after the approach path, after the runway path, and never on. Similarly, the heating can be turned off after cutting, before the overtravel path, after the overtravel path, and never off. This level of control enables the production of tab-free layups, which are important for many reasons.
Tabs are essentially non-bonded tapes at the border of the layup area. They are usually a waste of material and require increased post-processing. Additionally, such tabs prevent the selective reinforcement capability of the AFP process. By eliminating tabs, the AFP-XS enables near-net shape layup, saves material, and provides selective reinforcement capability. Overall, the improved turning and on/off control provided by the AFP-XS is a game changer for composite manufacturing, enabling higher-quality parts and greater efficiency.
Thermoplastic tapes require uniform heating for better bonding, and flashlamps are an effective way to provide this heating for ergonomic operation, where a human can be near the process. However, running an AFP system with a flashlamp requires keeping the flashlamp at a 2-3mm range to ensure uniform heating for the thermoplastic composite layup. This is where the built-in tilt control of the AFP-XS comes in.
With the new functionality called tool tilt control, the AFP-XS provides fine-level control at the layup level, layer level, each tape level, and at each frame level. This control enables the flashlamp to be brought very close to the tape and layup without any collision, providing the uniform heating required for high-quality bonding.
The importance of higher exposure for high-temperature thermoplastic layup cannot be overstated. By adding additional tilt, the light-emitting area of the flash lamp is able to heat the tape more gradually, enabling a much better bond quality. The benefits of higher exposure for thermoplastic composite parts include uniform heating over a wide speed/acceleration range, better bonding across the layup, and ultimately, higher-quality composite parts.
Overall, the built-in tilt control of the AFP-XS is a crucial feature for a high-temperature thermoplastic layup, providing fine-level control to bring the flashlamp close to the tape and layup without any collision, and enabling uniform heating for high-quality bonding.
The AFP-XS by Addcomposites is designed to provide a cooled compaction roller with internal cooling to ensure longevity and reduce downtime during composite manufacturing. The system utilizes the existing cooling source from the AFP-XS system and cools down the compaction roller, reducing its temperature and enabling continual operation.
The importance of longevity for the compaction roller in composite manufacturing cannot be overstated. The compaction roller plays a critical role in the AFP process, ensuring consistent, high-quality layups. With a longer-lasting compaction roller, manufacturers can expect a longer operational shift of the AFP layup process without pausing for the roller to cool down. This not only increases efficiency but also ensures a more consistent and higher-quality layup process.
The benefits of a longer-lasting compaction roller for composite parts are numerous. The longer life of the compaction roller provides a more consistently higher quality layup, reducing the likelihood of errors and defects in the final composite part. Additionally, the longer life of the compaction roller translates to less downtime and maintenance, improving the overall efficiency of the composite manufacturing process.
Thermoplastic composites are increasingly being used in a wide range of applications, from aerospace to automotive and beyond, due to their superior strength, durability, and weight-saving properties. However, producing high-quality thermoplastic composite parts requires precision and control at every step of the manufacturing process. The Automated Fiber Placement (AFP) process by Addcomposites has been instrumental in achieving this precision and control, and the latest version, the AFP-XS, has brought even more advancements in the field. In this blog post, we will explore three key features of the AFP-XS that have improved the controls and quality of thermoplastic composite parts: improved turning and on/off control for a tab-free layup, built-in tilt control for higher exposure and high-temperature thermoplastic layup, and a cooled compaction roller for longevity. Let's dive in!
The AFP-XS by Addcomposites is designed to provide improved turning and on/off control for a tab-free layup. Usually, in order to avoid the burning of the compaction roller or sudden heating of the initial portion of the tab, tapes are fed without any heat. However, with the heating control setup provided by AddPath, the AFP-XS enables millisecond level control of delay to heat the initial tapes exactly at the point that allows for the right amount of heating of the tabs and not burn the roller, eliminating the need for tabs.
The heating control allows for triggering heating on and off at each step of the program, with built-in delays to ensure precise control. These steps include before the approach path, after the approach path, after the runway path, and never on. Similarly, the heating can be turned off after cutting, before the overtravel path, after the overtravel path, and never off. This level of control enables the production of tab-free layups, which are important for many reasons.
Tabs are essentially non-bonded tapes at the border of the layup area. They are usually a waste of material and require increased post-processing. Additionally, such tabs prevent the selective reinforcement capability of the AFP process. By eliminating tabs, the AFP-XS enables near-net shape layup, saves material, and provides selective reinforcement capability. Overall, the improved turning and on/off control provided by the AFP-XS is a game changer for composite manufacturing, enabling higher-quality parts and greater efficiency.
Thermoplastic tapes require uniform heating for better bonding, and flashlamps are an effective way to provide this heating for ergonomic operation, where a human can be near the process. However, running an AFP system with a flashlamp requires keeping the flashlamp at a 2-3mm range to ensure uniform heating for the thermoplastic composite layup. This is where the built-in tilt control of the AFP-XS comes in.
With the new functionality called tool tilt control, the AFP-XS provides fine-level control at the layup level, layer level, each tape level, and at each frame level. This control enables the flashlamp to be brought very close to the tape and layup without any collision, providing the uniform heating required for high-quality bonding.
The importance of higher exposure for high-temperature thermoplastic layup cannot be overstated. By adding additional tilt, the light-emitting area of the flash lamp is able to heat the tape more gradually, enabling a much better bond quality. The benefits of higher exposure for thermoplastic composite parts include uniform heating over a wide speed/acceleration range, better bonding across the layup, and ultimately, higher-quality composite parts.
Overall, the built-in tilt control of the AFP-XS is a crucial feature for a high-temperature thermoplastic layup, providing fine-level control to bring the flashlamp close to the tape and layup without any collision, and enabling uniform heating for high-quality bonding.
The AFP-XS by Addcomposites is designed to provide a cooled compaction roller with internal cooling to ensure longevity and reduce downtime during composite manufacturing. The system utilizes the existing cooling source from the AFP-XS system and cools down the compaction roller, reducing its temperature and enabling continual operation.
The importance of longevity for the compaction roller in composite manufacturing cannot be overstated. The compaction roller plays a critical role in the AFP process, ensuring consistent, high-quality layups. With a longer-lasting compaction roller, manufacturers can expect a longer operational shift of the AFP layup process without pausing for the roller to cool down. This not only increases efficiency but also ensures a more consistent and higher-quality layup process.
The benefits of a longer-lasting compaction roller for composite parts are numerous. The longer life of the compaction roller provides a more consistently higher quality layup, reducing the likelihood of errors and defects in the final composite part. Additionally, the longer life of the compaction roller translates to less downtime and maintenance, improving the overall efficiency of the composite manufacturing process.