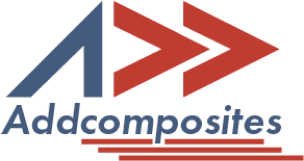
This blog is based on the article "Hydrogen Permeability of Thermoplastic Composites and Liner Systems for Future Mobility Applications" By Jan Condé-Wolter and team. Jan Condé-Wolter, along with his esteemed team, delves deep into the realm of thermoplastic composites, exploring their potential in the hydrogen economy. With a focus on hydrogen permeability, this comprehensive research provides pivotal insights that are set to shape the future of mobility applications. Drawing from rigorous experimentation and analysis, Condé-Wolter's work stands as a testament to the promise and challenges of thermoplastic composites in the rapidly evolving world of hydrogen storage and transportation. This article is a must-read for industry enthusiasts and researchers aiming to stay at the forefront of composite material innovations.
Hydrogen permeability in materials, especially thermoplastic composites, is a critical aspect to explore, particularly in the context of storage and transportation applications. The permeability of hydrogen through a material involves several mechanisms, including the absorption of the gas into the material, diffusion through it, and desorption out of the material.
The article discusses the use of materials with low solubility for the gas to be stored, which reduces the processes of absorption and desorption, thereby reducing overall permeation. Additionally, diffusion can be influenced by adding impermeable fillers like fibers or nanoparticles, which reduce the surface to be permeated and cause tortuous paths, increasing the length of the diffusion path and thus reducing permeation.
The article conducts high-pressure hydrogen permeation tests and measures specific permeation rates of various thermoplastic matrix materials as well as continuous fiber-reinforced thermoplastic composites (such as PA6, PA12, PA410, PPA, PPS), considering non-crimp and crimp textile architectures. Furthermore, liners based on thermoplastic high-barrier films made of EVOH (ethylene vinyl alcohol copolymers) were applied on PA6 composites, and their effect on permeation rate was investigated. EVOH is highlighted as one of the best-performing polymeric materials regarding permeation barrier due to its higher polyvinyl alcohol (PVA) content, which increases its polarity, decreasing the permeability of non-polar gases like hydrogen by limiting their solubility. However, as EVOH tends to swell and absorb water, which affects permeability negatively, it is often used in a multi-layer design to reduce water uptake and maintain permeation properties.
The research meticulously explores various thermoplastic matrix materials and continuous fiber-reinforced thermoplastic composites, conducting high-pressure hydrogen permeation tests to measure specific permeation rates. Some of the key samples investigated include:
These samples were subjected to various tests and analyses to understand their hydrogen permeability under different conditions and configurations. The research also explores the impact of using liners based on thermoplastic high-barrier films made of EVOH on PA6 composites and investigates their effect on permeation rate.
The methodology adopted in the research is thorough and systematic, ensuring accurate and reliable results. Here’s a simplified breakdown:
The research meticulously evaluates permeation data, ensuring a comprehensive understanding of the hydrogen permeability of various materials and configurations. The time between passing light barriers is measured, and since the volume in between is constant, a leakage rate Q (in ml/h) is measured directly. The duration of the experiment and the beginning of the steady state were determined manually by a test engineer. To reduce human bias, a uniform evaluation method was applied to all measured raw data, and no mean value was calculated over the manually determined steady-state. An example of this method is shown with the data of the #10 PPS sample in Figure.
A sigmoid function with its coefficients a, b, and c is a regression fit to the collected data using the least square method:
Each regression fit shows a sufficient coefficient of determination (r-square) above 0.91. As the function passes through the zero point and asymptotically approaches a limit value, it shows two physical characteristics of leakage measurements over time and is a suitable and simple approximation. The beginning of the steady-state was defined as the first data point reaching 95% of the steady-state value of the regression fit, which can be represented by the fraction of coefficients a and b:
Data points in the lag time before reaching the steady state are marked with red X as non-steady-state values, while all measuring points in the steady state are marked with a green circle. This methodology, involving the evaluation of permeation data and the utilization of a sigmoid function and regression fit, ensures a thorough and systematic analysis of the hydrogen permeability of various thermoplastic composites and liner systems, providing valuable insights and data for further research and application in future mobility applications.
The research embarked on a comprehensive exploration of the hydrogen permeability of various thermoplastic composites and liner systems, providing pivotal insights for future mobility applications. The study involved a meticulous analysis of several samples, such as #4-PA410-CF, #5-PPS-CF, #6-PPA-CF-A, #7-PPA-CF-B, #8-PPA-CF-C, #9-PA-6, #10-PPS, and #11-PPA, under high-pressure hydrogen permeation tests. The findings reveal that thermoplastic composites exhibit sufficient hydrogen barrier properties and can be amalgamated with robust thermoplastic liner materials. The results also underscore the importance of investigating the damage behavior of thermoplastics, as some samples exhibited transverse cracks without external load, leading to significant leakage rates.
The findings from the study have several potential implications in the industry, particularly in the development and optimization of materials and configurations for hydrogen storage and transportation applications. Here are a few key points:
Discover the future of composite manufacturing with Addcomposites! Here's how you can get involved:
At Addcomposites, we are dedicated to revolutionizing composite manufacturing. Our AFP systems and comprehensive support services are waiting for you to harness. So, don't wait – get started on your journey to the future of manufacturing today!
This blog is based on the article "Hydrogen Permeability of Thermoplastic Composites and Liner Systems for Future Mobility Applications" By Jan Condé-Wolter and team. Jan Condé-Wolter, along with his esteemed team, delves deep into the realm of thermoplastic composites, exploring their potential in the hydrogen economy. With a focus on hydrogen permeability, this comprehensive research provides pivotal insights that are set to shape the future of mobility applications. Drawing from rigorous experimentation and analysis, Condé-Wolter's work stands as a testament to the promise and challenges of thermoplastic composites in the rapidly evolving world of hydrogen storage and transportation. This article is a must-read for industry enthusiasts and researchers aiming to stay at the forefront of composite material innovations.
Hydrogen permeability in materials, especially thermoplastic composites, is a critical aspect to explore, particularly in the context of storage and transportation applications. The permeability of hydrogen through a material involves several mechanisms, including the absorption of the gas into the material, diffusion through it, and desorption out of the material.
The article discusses the use of materials with low solubility for the gas to be stored, which reduces the processes of absorption and desorption, thereby reducing overall permeation. Additionally, diffusion can be influenced by adding impermeable fillers like fibers or nanoparticles, which reduce the surface to be permeated and cause tortuous paths, increasing the length of the diffusion path and thus reducing permeation.
The article conducts high-pressure hydrogen permeation tests and measures specific permeation rates of various thermoplastic matrix materials as well as continuous fiber-reinforced thermoplastic composites (such as PA6, PA12, PA410, PPA, PPS), considering non-crimp and crimp textile architectures. Furthermore, liners based on thermoplastic high-barrier films made of EVOH (ethylene vinyl alcohol copolymers) were applied on PA6 composites, and their effect on permeation rate was investigated. EVOH is highlighted as one of the best-performing polymeric materials regarding permeation barrier due to its higher polyvinyl alcohol (PVA) content, which increases its polarity, decreasing the permeability of non-polar gases like hydrogen by limiting their solubility. However, as EVOH tends to swell and absorb water, which affects permeability negatively, it is often used in a multi-layer design to reduce water uptake and maintain permeation properties.
The research meticulously explores various thermoplastic matrix materials and continuous fiber-reinforced thermoplastic composites, conducting high-pressure hydrogen permeation tests to measure specific permeation rates. Some of the key samples investigated include:
These samples were subjected to various tests and analyses to understand their hydrogen permeability under different conditions and configurations. The research also explores the impact of using liners based on thermoplastic high-barrier films made of EVOH on PA6 composites and investigates their effect on permeation rate.
The methodology adopted in the research is thorough and systematic, ensuring accurate and reliable results. Here’s a simplified breakdown:
The research meticulously evaluates permeation data, ensuring a comprehensive understanding of the hydrogen permeability of various materials and configurations. The time between passing light barriers is measured, and since the volume in between is constant, a leakage rate Q (in ml/h) is measured directly. The duration of the experiment and the beginning of the steady state were determined manually by a test engineer. To reduce human bias, a uniform evaluation method was applied to all measured raw data, and no mean value was calculated over the manually determined steady-state. An example of this method is shown with the data of the #10 PPS sample in Figure.
A sigmoid function with its coefficients a, b, and c is a regression fit to the collected data using the least square method:
Each regression fit shows a sufficient coefficient of determination (r-square) above 0.91. As the function passes through the zero point and asymptotically approaches a limit value, it shows two physical characteristics of leakage measurements over time and is a suitable and simple approximation. The beginning of the steady-state was defined as the first data point reaching 95% of the steady-state value of the regression fit, which can be represented by the fraction of coefficients a and b:
Data points in the lag time before reaching the steady state are marked with red X as non-steady-state values, while all measuring points in the steady state are marked with a green circle. This methodology, involving the evaluation of permeation data and the utilization of a sigmoid function and regression fit, ensures a thorough and systematic analysis of the hydrogen permeability of various thermoplastic composites and liner systems, providing valuable insights and data for further research and application in future mobility applications.
The research embarked on a comprehensive exploration of the hydrogen permeability of various thermoplastic composites and liner systems, providing pivotal insights for future mobility applications. The study involved a meticulous analysis of several samples, such as #4-PA410-CF, #5-PPS-CF, #6-PPA-CF-A, #7-PPA-CF-B, #8-PPA-CF-C, #9-PA-6, #10-PPS, and #11-PPA, under high-pressure hydrogen permeation tests. The findings reveal that thermoplastic composites exhibit sufficient hydrogen barrier properties and can be amalgamated with robust thermoplastic liner materials. The results also underscore the importance of investigating the damage behavior of thermoplastics, as some samples exhibited transverse cracks without external load, leading to significant leakage rates.
The findings from the study have several potential implications in the industry, particularly in the development and optimization of materials and configurations for hydrogen storage and transportation applications. Here are a few key points:
Discover the future of composite manufacturing with Addcomposites! Here's how you can get involved:
At Addcomposites, we are dedicated to revolutionizing composite manufacturing. Our AFP systems and comprehensive support services are waiting for you to harness. So, don't wait – get started on your journey to the future of manufacturing today!