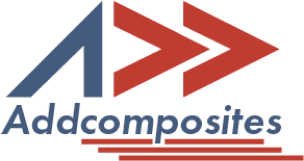
Have you ever wondered how the future of solar-powered vehicles is being shaped by advanced manufacturing techniques? 🤔 The development of a hybrid composite wheel for the Sunswift 7 solar car demonstrates a pivotal leap forward, blending automated fibre placement (AFP) with hand layup methods for unparalleled weight reduction and strength. 🌞🚗
This blog post delves into the innovative process behind creating a lighter, more durable wheel that could set new standards for vehicle performance and efficiency. From the limitations of traditional manufacturing to the cutting-edge AFP technology, discover how this project is driving the future of eco-friendly transportation. 🌱
1️⃣ Innovation in Wheel Manufacturing: Discover the blend of AFP and hand layup methods. 🛠
2️⃣ Beyond Traditional Limits: How new techniques overcome old challenges. 🚫🏭
3️⃣ Precision and Performance: The role of AFP in creating optimal strength-to-weight ratios. ⚖️💪
4️⃣ Sustainability Meets Efficiency: A glimpse into the future of eco-friendly transport. 🌍➡️🚀
5️⃣ Validation Through Rigorous Testing: Ensuring the wheel's performance matches theoretical predictions. ✅🔍
Embark on a journey through the advancements in solar-powered vehicle technology and see how innovation is steering us towards a sustainable future. 🌟
In the realm of high-performance vehicles, especially solar-powered cars, the quest for efficiency is paramount, with weight reduction playing a pivotal role. The wheel, a crucial component, significantly influences a vehicle's range, handling, and acceleration. This blog delves into the development of a groundbreaking hybrid composite wheel designed for the Sunswift 7 solar car. By marrying automated fibre placement (AFP) with traditional hand layup techniques, this project not only addresses the challenges inherent in traditional wheel manufacturing but also paves the way for a new era of lightweight, durable vehicle components. Through meticulous design, rigorous analysis, and innovative manufacturing, a wheel that stands at the intersection of technology and sustainability was born, setting a new standard for the automotive industry.
Traditional wheel manufacturing methods face significant challenges in meeting the advanced needs of solar-powered vehicles, particularly in achieving the optimal balance between lightweight construction and the requisite strength. Conventional processes often fall short in several key areas:
By contrast, the development of the hybrid composite wheel for the Sunswift 7 solar car, utilizing automated fibre placement (AFP) and hand layup, addresses these limitations head-on. This innovative approach allows for precise material placement, optimization of the strength-to-weight ratio, and reduced environmental impact, setting a new standard for wheel manufacturing in high-performance vehicles.
The development of a hybrid composite wheel for the Sunswift 7 solar car represents a significant leap forward in wheel manufacturing technology. This process combines the precision of Automated Fibre Placement (AFP) with the versatility of hand layup techniques, embodying a synergistic approach to crafting wheels that are both lightweight and strong. Here’s how this innovative process unfolds:
This method is pivotal for creating the wheel disc, enabling selective reinforcement through strategically placed spokes. AFP allows for precise control over fibre orientation and placement, optimizing the structural integrity and minimizing material waste. The use of Path planning software ensures that fibre paths are optimized, significantly reducing overlaps and enhancing performance.
For areas requiring intricate shaping and placement, such as the rim and tyre mounting region, hand layup proves invaluable. This technique provides the flexibility needed to address complex geometrical challenges, ensuring that every component of the wheel conforms to the highest standards of strength and weight efficiency.
Utilizing the ANSYS ACP PrepPost suite, the wheel undergoes rigorous numerical analysis to ensure that the design is not only optimized for weight but also meets the stringent strength requirements necessary for high-performance applications. This stage involves detailed simulations to predict and enhance the wheel's response to real-world loading conditions.
Through a combination of theoretical analysis and empirical testing, the wheel design is refined to achieve an ideal balance between weight and durability. The final product undergoes mechanical testing to verify its performance, with results closely aligning with the predicted outcomes.
The culmination of this project is the successful creation of a hybrid composite wheel for the Sunswift 7 solar car, a testament to the ingenuity and efficacy of combining automated fibre placement (AFP) with hand layup techniques. This section delves into the critical phases of manufacturing, integration, and validation:
Discover the future of composite manufacturing with Addcomposites! Here's how you can get involved:
At Addcomposites, we are dedicated to revolutionizing composite manufacturing. Our AFP systems and comprehensive support services are waiting for you to harness. So, don't wait – get started on your journey to the future of manufacturing today!
Have you ever wondered how the future of solar-powered vehicles is being shaped by advanced manufacturing techniques? 🤔 The development of a hybrid composite wheel for the Sunswift 7 solar car demonstrates a pivotal leap forward, blending automated fibre placement (AFP) with hand layup methods for unparalleled weight reduction and strength. 🌞🚗
This blog post delves into the innovative process behind creating a lighter, more durable wheel that could set new standards for vehicle performance and efficiency. From the limitations of traditional manufacturing to the cutting-edge AFP technology, discover how this project is driving the future of eco-friendly transportation. 🌱
1️⃣ Innovation in Wheel Manufacturing: Discover the blend of AFP and hand layup methods. 🛠
2️⃣ Beyond Traditional Limits: How new techniques overcome old challenges. 🚫🏭
3️⃣ Precision and Performance: The role of AFP in creating optimal strength-to-weight ratios. ⚖️💪
4️⃣ Sustainability Meets Efficiency: A glimpse into the future of eco-friendly transport. 🌍➡️🚀
5️⃣ Validation Through Rigorous Testing: Ensuring the wheel's performance matches theoretical predictions. ✅🔍
Embark on a journey through the advancements in solar-powered vehicle technology and see how innovation is steering us towards a sustainable future. 🌟
In the realm of high-performance vehicles, especially solar-powered cars, the quest for efficiency is paramount, with weight reduction playing a pivotal role. The wheel, a crucial component, significantly influences a vehicle's range, handling, and acceleration. This blog delves into the development of a groundbreaking hybrid composite wheel designed for the Sunswift 7 solar car. By marrying automated fibre placement (AFP) with traditional hand layup techniques, this project not only addresses the challenges inherent in traditional wheel manufacturing but also paves the way for a new era of lightweight, durable vehicle components. Through meticulous design, rigorous analysis, and innovative manufacturing, a wheel that stands at the intersection of technology and sustainability was born, setting a new standard for the automotive industry.
Traditional wheel manufacturing methods face significant challenges in meeting the advanced needs of solar-powered vehicles, particularly in achieving the optimal balance between lightweight construction and the requisite strength. Conventional processes often fall short in several key areas:
By contrast, the development of the hybrid composite wheel for the Sunswift 7 solar car, utilizing automated fibre placement (AFP) and hand layup, addresses these limitations head-on. This innovative approach allows for precise material placement, optimization of the strength-to-weight ratio, and reduced environmental impact, setting a new standard for wheel manufacturing in high-performance vehicles.
The development of a hybrid composite wheel for the Sunswift 7 solar car represents a significant leap forward in wheel manufacturing technology. This process combines the precision of Automated Fibre Placement (AFP) with the versatility of hand layup techniques, embodying a synergistic approach to crafting wheels that are both lightweight and strong. Here’s how this innovative process unfolds:
This method is pivotal for creating the wheel disc, enabling selective reinforcement through strategically placed spokes. AFP allows for precise control over fibre orientation and placement, optimizing the structural integrity and minimizing material waste. The use of Path planning software ensures that fibre paths are optimized, significantly reducing overlaps and enhancing performance.
For areas requiring intricate shaping and placement, such as the rim and tyre mounting region, hand layup proves invaluable. This technique provides the flexibility needed to address complex geometrical challenges, ensuring that every component of the wheel conforms to the highest standards of strength and weight efficiency.
Utilizing the ANSYS ACP PrepPost suite, the wheel undergoes rigorous numerical analysis to ensure that the design is not only optimized for weight but also meets the stringent strength requirements necessary for high-performance applications. This stage involves detailed simulations to predict and enhance the wheel's response to real-world loading conditions.
Through a combination of theoretical analysis and empirical testing, the wheel design is refined to achieve an ideal balance between weight and durability. The final product undergoes mechanical testing to verify its performance, with results closely aligning with the predicted outcomes.
The culmination of this project is the successful creation of a hybrid composite wheel for the Sunswift 7 solar car, a testament to the ingenuity and efficacy of combining automated fibre placement (AFP) with hand layup techniques. This section delves into the critical phases of manufacturing, integration, and validation:
Discover the future of composite manufacturing with Addcomposites! Here's how you can get involved:
At Addcomposites, we are dedicated to revolutionizing composite manufacturing. Our AFP systems and comprehensive support services are waiting for you to harness. So, don't wait – get started on your journey to the future of manufacturing today!