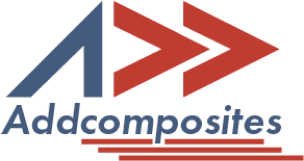
Continuous Fiber
A continuous fiber is geometrically characterized as having a very high length-to-diameter ratio. They are generally stronger and stiffer than bulk material. Fiber diameters generally range between 3-200 μm, depending upon the fiber
Composites
A composite material can be defined as a combination of two or more materials that
results in better properties than those of the individual components used alone, each material retains its separate chemical, physical, and mechanical properties. The two constituents are reinforcement and a matrix. The main advantages of composite materials are their high strength and stiffness, combined with low density, when compared with bulk materials, allowing for a weight reduction in the finished part.
Manufacturing with Robotic Programming
An industrial robot is a robot system used for manufacturing. Industrial robots are automated, programmable, and capable of movement on three or more axes.
Continuous Composites Manufacturing has two key widespread approaches. i.e. Automated Fiber Placement (AFP) and 3D Printing.
Continuous Fiber Composites: Automated Fiber Placement
In the AFP process, a band of continuous fiber tape is placed on the mold surface while being heated and pressed. This approach enables a very high strength to weight ratio along with selective fiber placement and fiber steering. In combination with 3D printing, an AFP can lay fiber on top of the 3-D printed tooling and cores, digitizing the complete production.
Continuous Fiber Composites: 3D Printing
Continuous fiber strands are coated in a curing agent and laid down into a thermoplastic matrix extruded via a print nozzle, there is no consolidation pressure applied. This results in high resin-rich areas, poor layer-to-layer bonding, and much lower fiber volume fraction.
A post-processing step can be applied to the 3D printed part to achieve the best possible Fiber Volume Fraction of ~ 1% porosity. However the post-consolidation through molds is only possible for relatively small parts.
A graphical representation
The graphical representation above comparing the different methods of continuous carbon fiber manufacturing depicts an elegant view of the manufacturing scenario.
1. CF 3D printing without consolidation enables larger prototype part printing
Image: Thermwood
2. CF 3D printing with consolidation enables smaller, yet functional, composites parts.
Image: 9T Labs
3. Automated Fiber Placement enables all sized functional composites parts
Image: Spirit Aerosystems
Conclusion
The 3D printing/AFP space with continuous composites is experiencing the innovation at multiple levels i.e. raw material, processing, manufacturing tools, software, inspection, and design, etc. All said, the future with composites manufacturing and robotics seems very promising for both smaller or bigger parts, and for prototypes or functional high-performance parts.
At Addcomposites we build accessible AFP tool heads, cells, robotic automation systems and simulation software. If you are looking for some collaborations, free trials, demos, or just want to know the price of things, feel free to reach out to James Kuligoski by emailing james.kuligoski@addcomposites.com.
Continuous Fiber
A continuous fiber is geometrically characterized as having a very high length-to-diameter ratio. They are generally stronger and stiffer than bulk material. Fiber diameters generally range between 3-200 μm, depending upon the fiber
Composites
A composite material can be defined as a combination of two or more materials that
results in better properties than those of the individual components used alone, each material retains its separate chemical, physical, and mechanical properties. The two constituents are reinforcement and a matrix. The main advantages of composite materials are their high strength and stiffness, combined with low density, when compared with bulk materials, allowing for a weight reduction in the finished part.
Manufacturing with Robotic Programming
An industrial robot is a robot system used for manufacturing. Industrial robots are automated, programmable, and capable of movement on three or more axes.
Continuous Composites Manufacturing has two key widespread approaches. i.e. Automated Fiber Placement (AFP) and 3D Printing.
Continuous Fiber Composites: Automated Fiber Placement
In the AFP process, a band of continuous fiber tape is placed on the mold surface while being heated and pressed. This approach enables a very high strength to weight ratio along with selective fiber placement and fiber steering. In combination with 3D printing, an AFP can lay fiber on top of the 3-D printed tooling and cores, digitizing the complete production.
Continuous Fiber Composites: 3D Printing
Continuous fiber strands are coated in a curing agent and laid down into a thermoplastic matrix extruded via a print nozzle, there is no consolidation pressure applied. This results in high resin-rich areas, poor layer-to-layer bonding, and much lower fiber volume fraction.
A post-processing step can be applied to the 3D printed part to achieve the best possible Fiber Volume Fraction of ~ 1% porosity. However the post-consolidation through molds is only possible for relatively small parts.
A graphical representation
The graphical representation above comparing the different methods of continuous carbon fiber manufacturing depicts an elegant view of the manufacturing scenario.
1. CF 3D printing without consolidation enables larger prototype part printing
Image: Thermwood
2. CF 3D printing with consolidation enables smaller, yet functional, composites parts.
Image: 9T Labs
3. Automated Fiber Placement enables all sized functional composites parts
Image: Spirit Aerosystems
Conclusion
The 3D printing/AFP space with continuous composites is experiencing the innovation at multiple levels i.e. raw material, processing, manufacturing tools, software, inspection, and design, etc. All said, the future with composites manufacturing and robotics seems very promising for both smaller or bigger parts, and for prototypes or functional high-performance parts.
At Addcomposites we build accessible AFP tool heads, cells, robotic automation systems and simulation software. If you are looking for some collaborations, free trials, demos, or just want to know the price of things, feel free to reach out to James Kuligoski by emailing james.kuligoski@addcomposites.com.