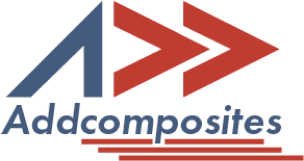
Automated Fiber Placement (AFP) is a computer-aided manufacturing process used for the fabrication of continuous fiber composites. It involves laying down strips of continuous fiber prepreg tapes on a tool, typically by a robot arm equipped with a fiber placement head. The tape is heated at the nip point, pressed onto the substrate, and then cut into specified lengths.
To operate AFP systems, operators need knowledge of composites processing and CNC machine operation. The process involves:
Criteria for AFP Suitability: Given the constraints and process details, components ideal for AFP should have:
Real-World Applications of AFP: Automated Fiber Placement systems are utilized in various industries, including:
Understanding the intricacies of the AFP process is crucial for its successful application. While it offers numerous benefits, it's essential to be aware of its constraints. By considering the specific requirements of a project and consulting with experts, one can harness the full potential of AFP for high-quality composite parts.
Discover the future of composite manufacturing with Addcomposites! Here's how you can get involved:
At Addcomposites, we are dedicated to revolutionizing composite manufacturing. Our AFP systems and comprehensive support services are waiting for you to harness. So, don't wait – get started on your journey to the future of manufacturing today!
Automated Fiber Placement (AFP) is a computer-aided manufacturing process used for the fabrication of continuous fiber composites. It involves laying down strips of continuous fiber prepreg tapes on a tool, typically by a robot arm equipped with a fiber placement head. The tape is heated at the nip point, pressed onto the substrate, and then cut into specified lengths.
To operate AFP systems, operators need knowledge of composites processing and CNC machine operation. The process involves:
Criteria for AFP Suitability: Given the constraints and process details, components ideal for AFP should have:
Real-World Applications of AFP: Automated Fiber Placement systems are utilized in various industries, including:
Understanding the intricacies of the AFP process is crucial for its successful application. While it offers numerous benefits, it's essential to be aware of its constraints. By considering the specific requirements of a project and consulting with experts, one can harness the full potential of AFP for high-quality composite parts.
Discover the future of composite manufacturing with Addcomposites! Here's how you can get involved:
At Addcomposites, we are dedicated to revolutionizing composite manufacturing. Our AFP systems and comprehensive support services are waiting for you to harness. So, don't wait – get started on your journey to the future of manufacturing today!