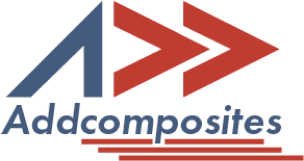
Today, fiber-reinforced composites are frequently used materials for structural applications in various industries e.g. marine, automotive, aerospace to sports. These composites are applied in two key ways to the production of advanced structures,
While producing such composite parts, there are several placement methods available. Among them, Automated Fiber Placement (AFP) is one of the most efficient and economic methods in the industry today.
AFP is a unique process where individual tapes, called tows, are pulled off spools and fed through a delivery system into a fiber placement head. These bands of tows, called a course, follow programmed fiber paths and is placed directly on to a mold or work surface to create a preform. The individual layers of the preforms experience in-situ consolidation (i.e. consolidated on the fly), whilst a number of heating systems (infrared, laser, flash lamps) are used to tack one layer to the other.
With the latest innovation in a compact automated fiber placement system from Addcomposites, it is now possible to achieve:
Today, fiber-reinforced composites are frequently used materials for structural applications in various industries e.g. marine, automotive, aerospace to sports. These composites are applied in two key ways to the production of advanced structures,
While producing such composite parts, there are several placement methods available. Among them, Automated Fiber Placement (AFP) is one of the most efficient and economic methods in the industry today.
AFP is a unique process where individual tapes, called tows, are pulled off spools and fed through a delivery system into a fiber placement head. These bands of tows, called a course, follow programmed fiber paths and is placed directly on to a mold or work surface to create a preform. The individual layers of the preforms experience in-situ consolidation (i.e. consolidated on the fly), whilst a number of heating systems (infrared, laser, flash lamps) are used to tack one layer to the other.
With the latest innovation in a compact automated fiber placement system from Addcomposites, it is now possible to achieve: